How to Control the Welding Deformation of Large Storage Tank Bottom Plate
Large storage tank is one of the indispensable equipment in petrochemical plant. The tank bottom plate bears more force than other parts of the whole storage tank, while the serious welding deformation of tank bottom can reduce the loading capacity and stability of storage tank. The storage tank bottom is welded by a plurality of bottom plate and annular plate, the quantity of welding seam is much, the welding stress is large, and it is easy to produce the welding deformation. Therefore, it is important to analyze the mechanism of storage tank bottom plate welding deformation and various influencing factors, to master the changing rules and to take effective measures to control the deformation of bottom plate, in order to ensure the installation quality of storage tank bottom. Taking 10 * 104 m3 oil tank as an example, the following article discusses the reasons and preventive measures of welding deformation of storage tank bottom plate.
Analysis of storage tank bottom plate welding deformation
The generation of welding deformation, fundamentally speaking, is the reason that the temperature distribution on the component is very uneven during the storage tank welding process, resulting in large contraction of high temperature area and small contraction of low temperature area after cooling, this uneven contraction leads to a change in the shape of the component. For a particular structure, the final deformation is related to the position of the welding and the contraction of the weld itself, In addition, a certain distribution of internal stress will be produced during the welding process, which will also affect the deformation of the component. Therefore, in order to control storage tank welding deformation, on the one hand, to increase the stiffness of the welded components or the external constraints of the component, on the other hand, try to reduce the uneven degree of welding temperature field, in order to reduce the deformation of the driving force.
Welding deformation of storage tank bottom plate can be roughly divided into seven forms: longitudinal contraction deformation, transverse contraction deformation, angular distortion, flexure deformation, wave deformation, butt joint deformation, and twisted. For welding deformation of large storage tank bottom plate, wave deformation and angular deformation are the main deformation form.
Angular deformation: produced in the situation of butt welding, lap welding, and T-joint welding. The fundamental reason is the uneven distribution of transverse contraction deformation in the thickness direction.
The front deformation of the weld seam is large, and the back deformation is small, thus the deflection of the component plane is formed. In butt welding, the difference of transverse contraction, which is caused by the difference metal cover on the upper and the lower part of the welded joint, causes the angular deformation.
Wave deformation: Stress exists in the plate after welding of thin plate, normally, the area near the weld seam is tensile stress, and the distance from the weld seam is compressive stress. Under the action of the compressive stress, the thin plate may be unstable, and the wave deformation can be produced. For bottom plate of large storage tank , the thickness of annular plate is larger, the length of weld seam is shorter; for center plates, if the center plate is not free to contract because of the external force during the welding, under the condition of no rigid fixation, the weld seam is made up and down, wave deformation inside the two sides of weld seam superimposes with it, the local arch at the bottom of whole storage up to tens of millimeters, it will not obey the requirement that the part deformation at bottom of the GB50128 storage tank can not exceed 50mm.
Storage tank structure and welding technology of 100,000 m³vertical oil tank bottom plate
Bottom plate of 100,000m³ storage tank is composed a bow shaped annular plate and center plate, annular plate is an arch shape, center plate is a polygonal flat plate structure that is composed of multiple plates, between the edge plate and bottom plate are welded together by shell joints, constitute the entire bottom plate. The bottom plate and wall plate are welded by feet weld seam. Material of annular plate is 12MnNiVR, material of center plate is Q235-B, the bottom plate structure is shown in figure 1.
Welding type is butt welding with bearing plate. Welding process adopts the technology that CO2 gas shielded arc welding to render and automatic submerged-arc welding to filling and copping.
Render: CHT711 Ф1.2 mm carbon dioxide welding wire.
Filling、capping: Broken wire HO8A Ф1.0 mm; submerged arc CHF431- HO8MnA; Welding flux: HJ431
Measures to control storage tank welding deformation
Select the reasonable arrangement of bottom plate
The layout of bottom plate is arranged according to the geometric size of the material. The common way of arrangement in China includes: Bar layout, mans shape layout, and tee shape layout. Through comparison, this project adopts T-shape plate layout method. Advantages are as following:
- Easy to arrangement when layout;
- To meet the welding conditions, easy to avoid making the plate in the welding stress over concentrated, and it can transmit the stress quickly and evenly, so as to overcome the phenomenon of Concave arch of bottom plate, which is caused by longitudinal and transverse contraction after welding of center plate.
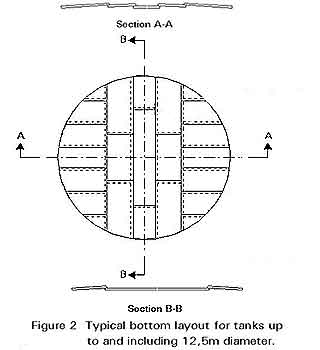
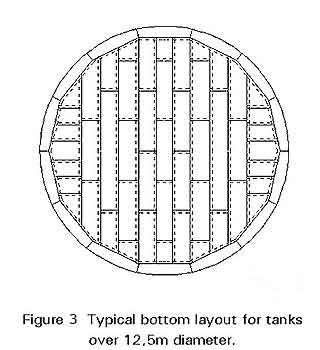
Control the pre- processing quality of bottom plate
The quality of pre-processing is the key factor that influences the tank bottom forming, during the pre-processing, the pre-process size of annular plate and center plate must meet the design requirements.
Cutting of small plates near the center plate adopts semi-automatic welding machine. Taking into account the contraction deformation of weld seam, obligate more 10mm at the side that lap joined with the annular plate, and weld it before weld the seam shell.
Reasonable storage tank welding sequence
Viewing from Fig.1 bottom plate arrangement of 100,000m³ storage tank, butt weld joint includes short weld seam and full-length weld seam, if the full-length weld seam is welded firstly, inner stress will be caused because that the rigidity will hinder the short seam welding contraction. So the short seam should be welded firstly, then full-length seam between the center plates. Shell joints and fillet weld are ring weld. The result of the contraction is equivalent to a uniform compressive stress applied to the inner region, under the action of this kind of compressive stress, the middle part of the bottom plate may be caused by the convex deformation. The welding process should be minimized on the contraction of the constraints, especially the Bighorn seam welding, welding must be within the limits of stiffness, The reason is that its circumference is very long, and its total shrinkage is the sum of its longitudinal contraction and transverse contraction. So after the fillet weld welding is completed, shell joint should be welded. After the above analysis, the tank bottom plate is in principle to take the following welding sequence.
Storage tank bottom plate welding sequence:
Short seam of center plate——full-length seam——300mm outside the annular plate——butt weld seam——fillet weld seam——Residual weld seam of annular plate——shell joint
By increasing the stiffness of components is an important measure to control the deformation, the center plate can be fixed by rigid method before welding, for example, fix both sides of the welding seam by the back bar, remove it after it is clod; for welding annular plates, install the wedge steel under the bearing plate to control the angle of reversible deformation in the range of 5~8 degree. When the environment temperature is high, the butt weld gap is small, and the thickness is large, reversible deformation is small, on the contrary, the reversible deformation is large. This is to compensate for the angular contraction of the weld and to control the angular distortion; for spot welding of shell joint, prevent welding deformation by rigid fixation of gantry plate.
Other measures to control storage tank welding deformation
- Under the premise of ensuring the quality of welding, as far as possible using a low welding current, smaller beveling gap and angle, quicker welding speed. Reduce the section area of welding and welding line energy, so as to reduce deformation and stress.
- After welding, forging by hammer along the weld and its heat affected zone, the direction of hammer is from outside to inside, the hammering point is gradually reduced from outside to inside. This is conducive to elongation, reduce stress.
- All of the welder should be certificated after the examination.
Conclusion
Although the bottom plate of storage tank is easy to deform after welding, as long as the reasonable welding process measures are taken, the welding quality of the bottom plate can be controlled effectively.